IoT predictive maintenance utilizes connected IoT devices to monitor machinery, collecting data like temperature and vibrations. By recognizing patterns, it forecasts potential breakdowns, enabling timely fixes. This approach reduces expenses and ensures smooth operations, transforming industry maintenance practices.

This article explains the basic concepts and key benefits of IoT predictive maintenance. It also explores some problems that IoT maintenance can solve proactively.
What is IoT Predictive Maintenance?
IoT predictive maintenance is an advanced strategy that uses IoT technology to collect and analyze data from sensors placed on equipment. This approach enhances maintenance efficiency by predicting potential issues before they cause downtime. Smart sensors monitor various parameters, transmitting real-time data to industrial IoT gateways and backend predictive maintenance software. This data is then analyzed to forecast equipment failures, enabling proactive maintenance. This strategy contrasts with reactive approaches, avoiding breakdowns by addressing faults in advance.
Original Equipment Manufacturers (OEMs) and solution providers are also integrating preventative maintenance capabilities into their products using IoT technologies, spanning a variety of industries from industrial equipment monitoring and light electric vehicles to IoT HVAC and energy sectors.
Benefits of IoT-based Predictive Maintenance
As various studies and reports demonstrate, the benefits of IoT-based predictive maintenance are significant and quantifiable. PwC and McKinsey published the quantitative data in their reports on IoT predictive maintenance, as highlighted in the following benefits.
Cost Reduction
Predictive maintenance can lead to a substantial reduction in maintenance costs. According to management consulting firm McKinsey, predictive maintenance has been reported to reduce expenses related to factory equipment by up to 40%.
Uptime Improvement
The implementation of IoT predictive maintenance can result in a significant improvement in uptime. PwC reports that, on average, IoT maintenance has improved uptime by 9%, ensuring that equipment remains operational for more productive hours.
Risk Reduction
Safety, health, environment, and quality risks can be diminished significantly through IoT predictive maintenance. PwC’s report suggests that companies can experience a 14% reduction in these risks by utilizing IoT maintenance strategies.
Asset Life Extension
IoT predictive maintenance can extend the life of aging assets. On average, companies can achieve an extension of up to 20% in the lifespan of their assets through the effective implementation of predictive maintenance practices.
Shorter Repair Times
IoT predictive maintenance can significantly reduce the time required to repair or recondition plant equipment. In a survey of 500 plants, the mean time to repair (MTTR) improved by 60% after one year of implementing IoT predictive maintenance management techniques.
Cost Savings from Spare Parts Management
IoT predictive maintenance can help to achieve a 30% decrease in the cost of stocking spare parts, as replacement parts are only stored when needed.
Increased Return on Investment (ROI)
IoT predictive maintenance can lead to a higher return on investment by reducing downtime, lowering maintenance expenses, and improving productivity. The improved revenue streams from production can contribute to a better ROI for companies.
IoT Predictive Maintenance Examples
The following concise use cases and examples for some problems demonstrate how IoT predictive maintenance can be applied across diverse industries to solve specific challenges, reduce downtime, and improve operational reliability.
Railway Track Health Monitoring
Problem: Poorly maintained tracks can result in accidents, service interruptions, and increased maintenance costs.
Solution: Install IoT sensors along railway tracks to monitor parameters like railway track alignment, stress, and temperature. When sending sensor data from rolling stock to the management center, which is housed in the middle or back office, 4G IoT gateways connect the data and guarantee its security. Any fault warning can advise the operation crew right away about preventive maintenance. Predictive algorithms process data to identify railway track anomalies. Alerts are sent for deviations, enabling timely railway track maintenance and ensuring safe operations.
Conveyor Belt System in a Manufacturing Plant
Problem: A manufacturing plant relies heavily on conveyor belt systems to transport materials between different stages of production. Unexpected breakdowns can lead to production delays and increased downtime.
Solution: Deploy vibration sensors along the conveyor belts to monitor the equipment’s health. Analyze the vibration patterns over time using predictive analytics. When abnormal vibration levels are detected, the system generates alerts, allowing maintenance teams to schedule maintenance before a failure occurs. This approach minimizes unplanned downtime and ensures uninterrupted production.
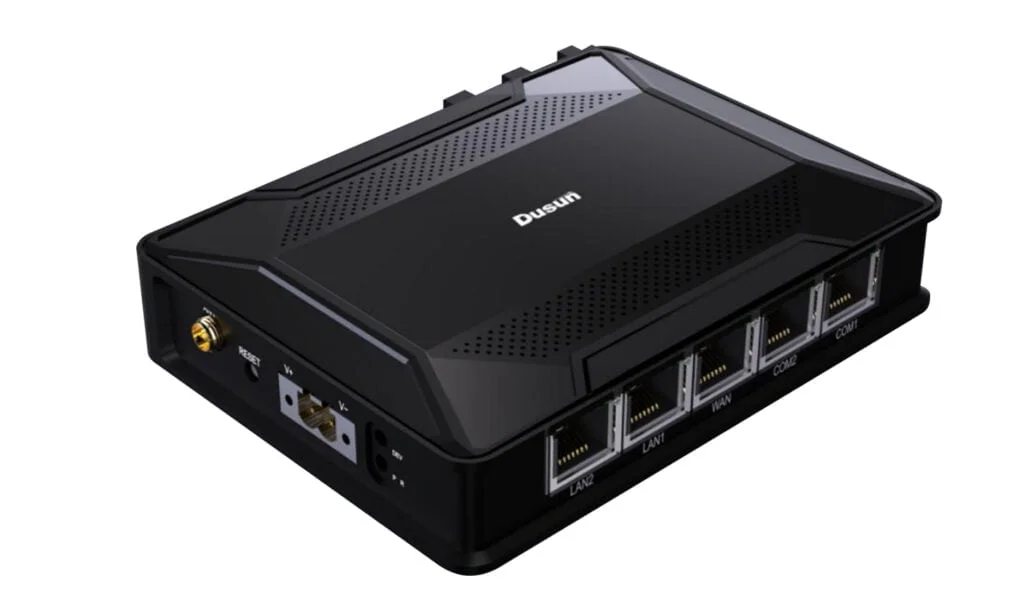
Pipeline Integrity in the Oil & Gas Sector
Problem: Pipeline leaks and integrity issues can result in environmental damage and financial losses.
Solution: Deploy IoT sensors along pipelines to monitor pressure, temperature, and corrosion levels. Machine learning algorithms analyze data to identify signs of corrosion or leakage. Alerts are generated for abnormal conditions, facilitating swift repairs and preventing leaks.

HVAC Systems in Commercial Buildings
Problem: Commercial buildings depend on HVAC systems for maintaining a comfortable environment. If these systems fail, it can result in discomfort for occupants and potential damage to sensitive equipment.

Solution: Install temperature, pressure, and humidity sensors in key locations of the HVAC system. If the temperature rises above a certain threshold or if there’s a pressure drop, the predictive maintenance solution triggers an alert.
Read further: IoT building automation control solution
Elevator Systems in a High-Rise Building
Problem: Frequent elevator breakdowns inconvenience tenants and visitors, affecting building functionality.
Solution: Install IoT sensors to monitor elevator motor vibrations and door operation. Predictive analytics can identify patterns of motor stress and door misalignment.
Read further: IoT elevator management using IIoT gateways
CNC Machines in a Manufacturing Facility
Problem: CNC machine breakdowns disrupt production schedules and impact manufacturing efficiency.
Solution: Equip CNC machines with IoT sensors that track parameters like motor performance and tool wear. Analytical models process data to predict tool deterioration. Alerts signal maintenance when tools are close to failure, allowing timely replacements and smooth production.
Solar Panels in a Solar Farm
Problem: Degraded solar panels reduce energy production and overall efficiency in a solar farm.
Solution: Install IoT sensors on solar panels to measure output voltage, current, and temperature. Data analysis detects drops in output efficiency. Alerts notify maintenance teams, enabling targeted panel cleaning or replacement to maintain optimal energy generation.
Read further: IoT-based solar panel monitoring
IoT Predictive Maintenance Solutions
The convergence of the Internet of Things (IoT) and predictive analytics has steered a paradigm shift in industrial maintenance. By seamlessly integrating a spectrum of advanced sensors, a pivotal IoT gateway, and cloud-based platforms, industries are empowered to harness data-driven insights for optimal maintenance strategies. This approach not only prevents disruptions but also maximizes operational efficiency. Let’s investigate the core components’ roles within IoT predictive maintenance solutions.
Smart Sensors
Sensors are the frontline data gatherers, finely tuned to capture critical data of equipment behavior. They come in diverse forms—vibration, temperature, acoustic, pressure, ultrasonic, and more—each attuned to detecting specific indicators of wear, anomalies, or potential failures. These sensors monitor and transmit real-time data from the equipment’s operational environment, forming the foundation of informed decision-making.
IoT Gateway
The Smart IoT gateway is the nerve center that bridges the gap between the sensor-rich edge and the intelligence of the cloud. Its multifaceted role is integral to the efficacy of the entire predictive maintenance ecosystem:

- Data Aggregation and Preprocessing: Operating at the edge, the IoT gateway aggregates and filters data from myriad sensors. It ensures that only relevant and condensed data traverse the bandwidth to the cloud.
- Communication Protocol Translation: Sensors often employ diverse communication protocols. The IoT gateway, an adept translator, harmonizes these protocols, creating a unified language for seamless communication across the spectrum of sensors. Explore protocol conversion gateway.
- Local Analysis and Real-time Responses: The IoT gateway isn’t merely a transmission tool; it also possesses localized computational capabilities. It can execute lightweight algorithms to detect immediate red flags, enabling real-time responses to critical events without latency-inducing round trips to the cloud.
- Security and Data Integrity: Equipped with encryption and authentication mechanisms, IoT gateway safeguards the integrity and confidentiality of the transmitted data.
Cloud Platform
The cloud platform is an intelligent hub with all the valuable data streams, paving the way for profound insights and strategic foresight.
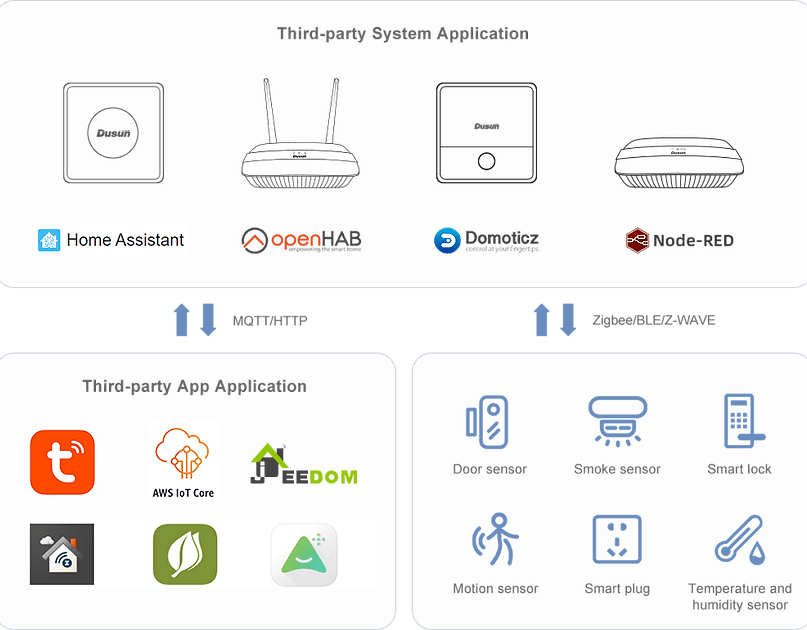
- Data Storage and Accessibility: The cloud offers ample storage, housing the data collected from sensors. It ensures accessibility and scalability, accommodating the expanding volume of data without constraints.
- Advanced Analytics and Pattern Recognition: Capitalizing on machine learning and predictive analytics, the cloud extracts patterns and trends from historical data. It observes subtle anomalies, projecting forthcoming failures and guiding IoT proactive maintenance.
- Visualization and Decision Support: The cloud empowers stakeholders with actionable insights by transforming raw data into intuitive visualizations. These visual cues aid in prompt decision-making, ensuring timely interventions.
- Collaboration and Scalability: The cloud’s collaborative work fosters the exchange of insights among teams regardless of geographic dispersion. Its scalability ensures that the IoT predictive maintenance infrastructure can evolve alongside the growing scope of operations.
FAQs of IoT Predictive Maintenance
What is industrial IoT predictive maintenance?
Industrial IoT predictive maintenance is a strategy that employs the Internet of Things (IoT) to collect real-time data from sensors and devices attached to industrial equipment. This data is then analyzed using advanced analytics and machine learning to predict potential equipment failures before they occur. This proactive approach enhances maintenance practices, reduces downtime, and improves operational efficiency.
What is the Architecture of IoT-Based Predictive Maintenance?
The architecture of IoT-based predictive maintenance typically involves several components:
- Sensors and Data Collection
- Data Transmission via IoT gateways
- Data Storage and Processing.
- Analytics and Prediction.
- Alerts and Notifications.
- Maintenance Action.
What are the Steps to Kick Start IoT-Based Predictive Maintenance?
Starting an IoT-based predictive maintenance program involves several key steps:
- Identify Equipment: Choose the equipment you want to monitor and maintain using IoT technology.
- Sensor Deployment: Install appropriate sensors on the chosen equipment to collect relevant data.
- Data Integration: Set up a data infrastructure to collect, store, and transmit sensor data to a central platform.
- Data Analytics: Implement analytics to process and analyze the collected data, identifying patterns and anomalies.
- Algorithm Development: Develop or select machine learning algorithms to predict equipment failures based on data patterns.
- Alert System: Implement a system to send alerts and notifications when potential failures are detected.
- Maintenance Planning: Use IoT predictive insights to plan and schedule maintenance activities proactively.