Why the continued investment? IoT-driven smart manufacturing, process automation and performance optimization for assets, plants, and operations are now top priorities. These innovations not only cut operational costs but also deliver impressive returns on investment (ROI).
In this article, we’ll dive into how IoT is revolutionizing smart manufacturing and explore the myriad benefits it brings to manufacturers. Let’s get started!
What Is Smart Manufacturing and The Role of IoT?
Concepts of smart manufacturing and industrial IoT is not brand new anymore. Essentially, it involves a network of interconnected devices and sensors that continuously collect and exchange data. The first example can be traced back to the 1960s when Procter & Gamble first used sensors in its soap factory to track product locations throughout the production process.
Today, IoT in the manufacturing industry makes data a new gold. Smart manufacturing leverages real-time data from machines and processes to optimize production and support informed decision-making, giving manufacturers a competitive edge.
In a nutshell, IoT in manufacturing provides these functions.
- Data Collection: Captures raw data from a network of smart sensors and machines, which would otherwise be inaccessible.
- Data Aggregation: Gathers data from diverse sources, including heterogeneous machines, sensors, legacy systems/hardware, modern systems, and other relevant devices, and send data to a centralized platform via IoT gateways.
- Data Enrichment: Analyzes and adds contextual information to the collected data.
- Data Visualization: Presents data in easily understandable formats.
- Actionable Insights: Converts data into actionable insights, enabling managers to implement effective optimization strategies.
Additionally, edge computing can automate certain tasks, reducing the need for human intervention and further optimizing production processes.
IoT in Manufacturing Examples
Predictive Maintenance
Traditionally, manufacturers would replace equipment parts at set intervals to mitigate the risk of failure and prevent production delays. This require dedicated maintenance personnel to regularly check equipment status and once there is a fault, the technicians need to plan maintenance and the production may be interrupted.
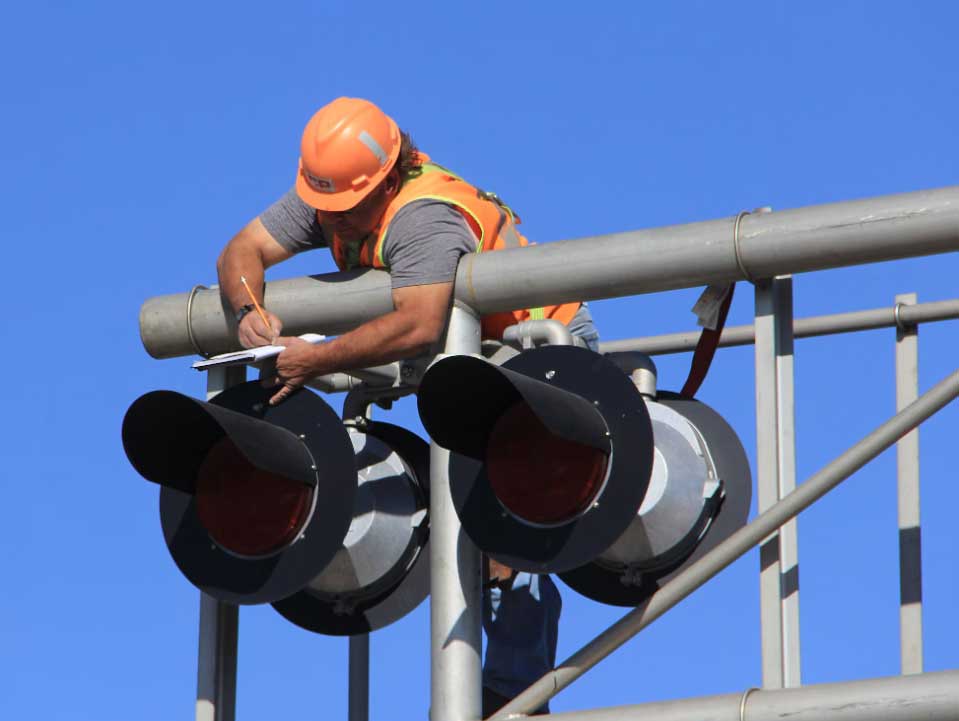
However, IoT technology now allows for real-time monitoring of machine conditions, ensuring maintenance is performed only when necessary. This approach not only lead to cost and time savings, but also enables technicians to schedule maintenance ahead of time to minimize production interruptions.
For example, Artesis, a company specializing in paper and pulp production equipment, adopted a predictive maintenance system using industrial IoT sensors. This implementation led to a 20% reduction in maintenance costs and a 10% increase in production efficiency.
Energy Management
IoT analytics offer valuable insights into energy consumption at the equipment and plant levels, helping to pinpoint areas where energy is wasted. This enables managers to seal the wastage loopholes, such as by reducing standby loads or preventing peak loads, to lower energy costs and environmental impacts.
Ford is a prime example of effective IoT energy management. The company installed IoT smart lights in its plants that adjust their brightness based on natural lighting conditions, resulting in annual energy savings of $4 million. Similarly, Armal, a portable toilet manufacturer, achieved nearly a 40% reduction in energy costs by implementing real-time IoT energy monitoring of their production lines.
Safety Improvement
Integrating sensors into industrial machines allows for real-time detection of potential safety hazards, such as excessive vibrations, overheating, or hazardous chemical leaks. IoT-enabled warning systems can automatically alert workers to these issues, significantly reducing the risk of costly or fatal accidents and minimizing downtime.
In addition, some companies equip employees with Bluetooth Low Energy (BLE) beacon cards to track their locations and prevent them from entering hazardous areas. This proactive approach enhances workplace safety by ensuring that workers are kept away from dangerous zones.
Impacts and Benefits of IoT in Smart Manufacturing
High Efficiency and Productivity
IoT provides valuable data, actionable insights, and automation that reduce waste, accelerate production, and enhance both yield output and quality.
Agility
Smart manufacturing and IoT can simplify product diversification by coordinating the production processes for all products and variants to run more efficiently and be manageable cost-wise.
Reduced Equipment Breakdown
Predictive maintenance driven by IoT minimizes the likelihood of equipment failures, lowers maintenance costs, and prevents extended downtimes.
Lower Energy Consumption and Costs
Monitoring the power drawn by production lines and machines in real time gives insights that can help optimize their consumption to lower utility costs.
Remote Troubleshooting
With IoT networks, high-level technicians can continue monitoring and troubleshooting industrial machines even after clocking out to keep the production processes optimal.
Supply Chain Optimization
IoT can play a significant role at the asset management level. It can manage inventory positions in warehouses and provide better visibility of the product when moving through the logistics network.
Increased Product Quality
By capturing data throughout the production process, manufacturers can determine which parameters are better for meeting the required quality specifications and customer requirements.
Enhanced Safety
IoT monitors various parameters, such as employee absence, near misses, and vehicle mishaps, during daily operations that can compromise employee safety.
Boosting Operational Intelligence
Edge computing in IoT introduces operational intelligence through automation and AIoT. Such solutions bring in intelligent communication and coordination with zero or minimal human input to optimize production.
IoT Devices for Smart Manufacturing
The IoT stack for smart manufacturing primarily comprises these four types of devices.
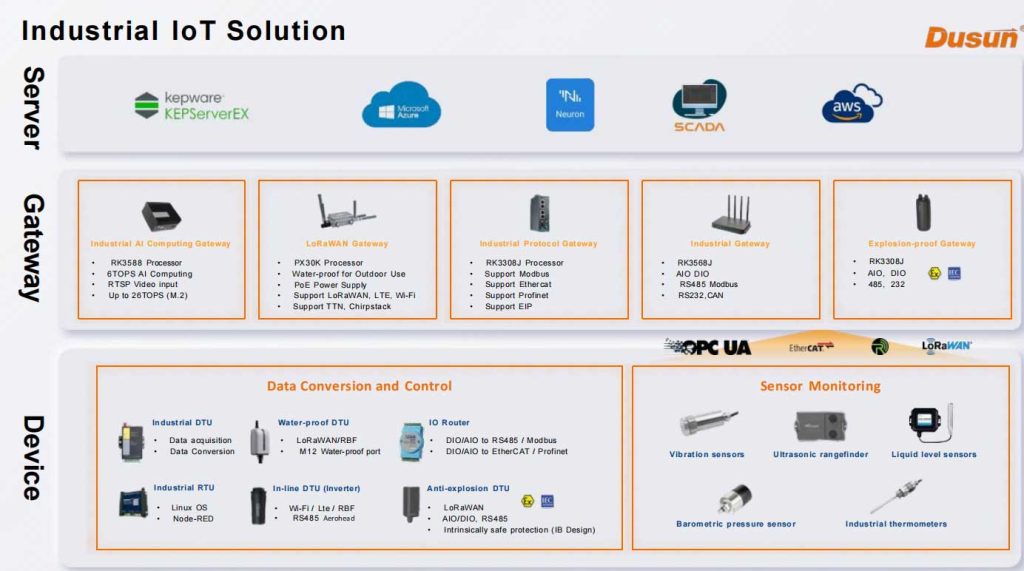
DTU
Data Transmission Units are critical in the smart manufacturing environment because they transmit RS232 and RS485 data wirelessly from remote devices to a central monitoring system or industrial gateways.
The device typically uses techniques like GPRS, GSM, 3G, 4G, or 5G to send the data, which eliminates the need to wire the industrial protocol communication across long distances. DTUs can also provide control operations via RTUs (Remote Terminal Units).
Also read: what is an industrial gateway?
Sensors
Sensors collect the actual data from the machines, equipment, and environment. Since this data is in analog form, the stack needs an RTU to convert the analog variables into digital data for serial transmission via RS232 or RS485.
So the arrangement starts with sensors connected to RTUs, then to DTUs and out to the gateway. But the DTU might not be necessary if you don’t need wireless transmission.
Gateway or Routers
Industrial gateways and routers collect and aggregate the data to transmit it to the cloud. DSGW-380 industrial 5G gateway with edge computing and light AI processing capabilities are becoming increasingly popular because they can automate tasks and provide analytics functions near the data source.
Servers (Local or Remote)
Servers provide the heavyweight analytics function to help in making informed decisions. Remote servers eliminate hefty installation costs and include platforms like AWS and Azure. On the other hand, local servers provide better data security because all communication remains within the LAN. Platforms like SCADA provide both remote and on-premise servers, so you can use the most suitable option.
IoT Technologies Used for IoT Manufacturing
5G
The 5th generation mobile network, or 5G, offers significantly faster upload and download speeds, increased bandwidth, and more reliable connections. This technology supports real-time, round-trip communication between DTUs, gateways, and remote servers, especially when wired connections are not available.
AIoT
AIoT represents the integration of Artificial Intelligence (AI) with IoT. This synergy allows edge devices to learn, adapt, and make autonomous decisions while performing light analytics on data from industrial sensors. This capability enhances the efficiency and intelligence of IoT manufacturing operations.

Edge Computing
With Industry 4.0 generating vast amounts of data, edge computing becomes crucial. It enables data storage, analysis, and processing closer to the data source, reducing latency and enhancing real-time decision-making capabilities.
Also read: what are edge computing devices?
Positioning
Positioning technologies are vital for tracking assets, particularly in transportation and logistics. In manufacturing, these technologies can optimize supply chains by equipping products with tags or using sensors to identify and address bottlenecks that lead to inefficiencies.
Also read: Bluetooth RSSI
Digital Twins
Digital twins are virtual replicas of physical assets and processes within the factory. By utilizing data from sensors, digital twins provide real-time insights into variables like temperature, color, and thickness. This virtual model allows managers and engineers to optimize production systems in near real-time, reducing costs, improving quality, and boosting productivity.
Challenges of IoT in Smart Manufacturing
Limited Interoperability
One of the significant challenges in implementing IoT in manufacturing is the lack of interoperability. Different companies use various communication protocols, closed-source operating systems, and programming languages, making it difficult to integrate systems seamlessly. Achieving effective IoT implementation often requires substantial effort and investment in both software and hardware (e.g. multi-protocol gateways) to bridge these compatibility gaps.
Data Security and Privacy
Data security and privacy are critical concerns in the Industrial Internet of Things (IIoT). The communication between edge devices and the cloud is vulnerable to cyber-attacks. If hackers gain access to these systems, they can steal or alter vital operational data, potentially compromising product quality and production integrity. Ensuring robust security measures like embedded security module, data encryption, user authentification, etc., are in place is essential to protect sensitive information and maintain operational reliability.
How Dusun IoT Solutions Help in IoT Manufacturing (Hardware-only)?
Dusun IoT offers vertically integrated hardware solutions, from gateways (edge devices) to end nodes, ensuring smooth operation of your IoT manufacturing processes.
Robust Gateways for Protocol Conversion and Connectivity
Our industrial IoT gateways, such as the DSGW-380 RK3588 industrial AI edge computing gateway, feature interfaces like RS232, RS485, CAN, and Gigabit Ethernet, supporting various industrial real-time Ethernet and Fieldbus protocols used in robotics, intelligent manufacturing automation, and smart infrastructure for Industry 4.0. These gateways also have SIM card slots for fast 5G connectivity and a 6 TOPs NPU on the RK3588 core for lightweight AI edge computing. They support LoRaWAN and other wireless protocols.
In addition to these powerful AI industrial computing gateways, we offer industrial LoRaWAN gateways, such as the DSGW-014 LoRaWAN outdoor gateway, which comes with industrial-grade waterproof housings for outdoor installations.

We also provide explosion-proof gateways/DTUs designed to withstand intense vibrations and harsh industrial conditions. Our industrial protocol gateway hubs support Modbus, EtherCAT, EIP, and Profinet, enabling protocol conversion in any smart manufacturing network.
End Nodes Customized from Powerful SoMs and SBCs
For end nodes, we provide embedded boards for sensors used for vibration, liquid level, barometric pressure, industrial thermometers, and ultrasonic rangefinders to collect data for analysis.
If you don’t want to run cables from these end nodes to the gateways or if the sensors are distributed far apart in the field, you can use either of our data conversion and control hardware to enable wireless communication. These include an industrial, waterproof, anti-explosion, or in-line (inverter) DTU, industrial RTU, or I/O router.
The DTUs can connect to SCADA systems, while the RTUs collect and aggregate signals from the sensors, convert them to digital signals, and transmit them to the DTUs. Some of our devices feature built-in integration with various cloud platforms like AWS, Azure, and ThingsBoard, making it easy to develop the analytics component. You can use such products to build complete, interoperable smart manufacturing solutions in minimal time.
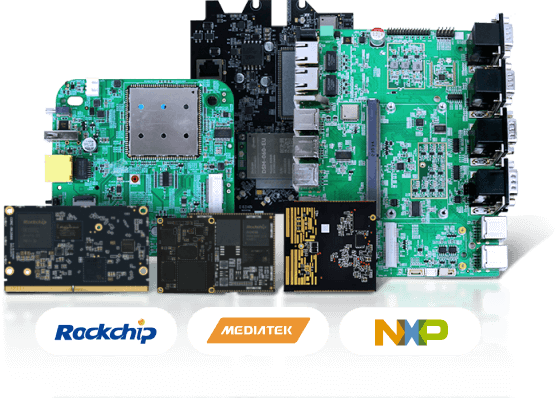
Case Study:
Using RK3588 SBC to develop AI cameras
Using RK3588J to develop mobile robots like AGV and AMR
Network and Device Security
To prevent safety issues, all our hardware support encryption algorithms like DES, RSA, and AES to secure communication.
Additionally, these devices provide edge computing to process most of the data locally and minimize the data going out. Some even have NPUs for AI computing to handle machine learning and complicated analytics tasks on the edge, then send only the essential data out.
Keeping data local enhances security and privacy, preventing tampering even if hackers gain access to the cloud link.
Cloud-SDK-integrated Gateway Solutions
Our industrial gateways come with built-in integration for cloud platforms like AWS, Azure, ThingsBoard and more. By leveraging Dusun IoT’s complete hardware solutions, you can build robust, interoperable IoT-based smart manufacturing infrastructure efficiently.
Wrapping Up
IoT in smart manufacturing is a lucrative business because it is still evolving, roping in more processes and machines to optimize the entire value chain. As a smart manufacturing IoT hardware solution provider, the future looks promising, and we can get in early to reap the benefits and acquire market share.
Partnering with us, you can focus on solution deployment while we supply the necessary hardware—both ready-made and ODM—to expedite your time to market. It’s important to note that smart manufacturing hardware solutions encompass more than gateways and end nodes. While these components form the core of IoT, Industry 4.0 also requires other industrial automation equipment, such as Human-Machine Interfaces (HMIs) and mobile robots (AGVs and AMRs).
We offer powerful System on Modules (SoMs) and embedded board custom services to help you build these automation tools.
For clients with existing traditional HMIs and want to upgrade them, consider our DSGK-061 smart VNX edge box (with VNC Virtual Network Computing remote control software) as a cost-effective alternative to replacement. This solution transforms HMIs into remote viewers. It also allows you to make secondary development, program your own applications and introduce new functions without affecting the original HMI’s system resources. The VNC edge box also adds more hardware interfaces for peripheral device connectivity, supports edge computing, and features a 1 TOPS NPU for lightweight AI computing.
Want to get started with Industry 4.0 smart manufacturing IoT solutions? Send us your details, and we’ll be in touch to discuss the technical aspects and pricing ASAP.